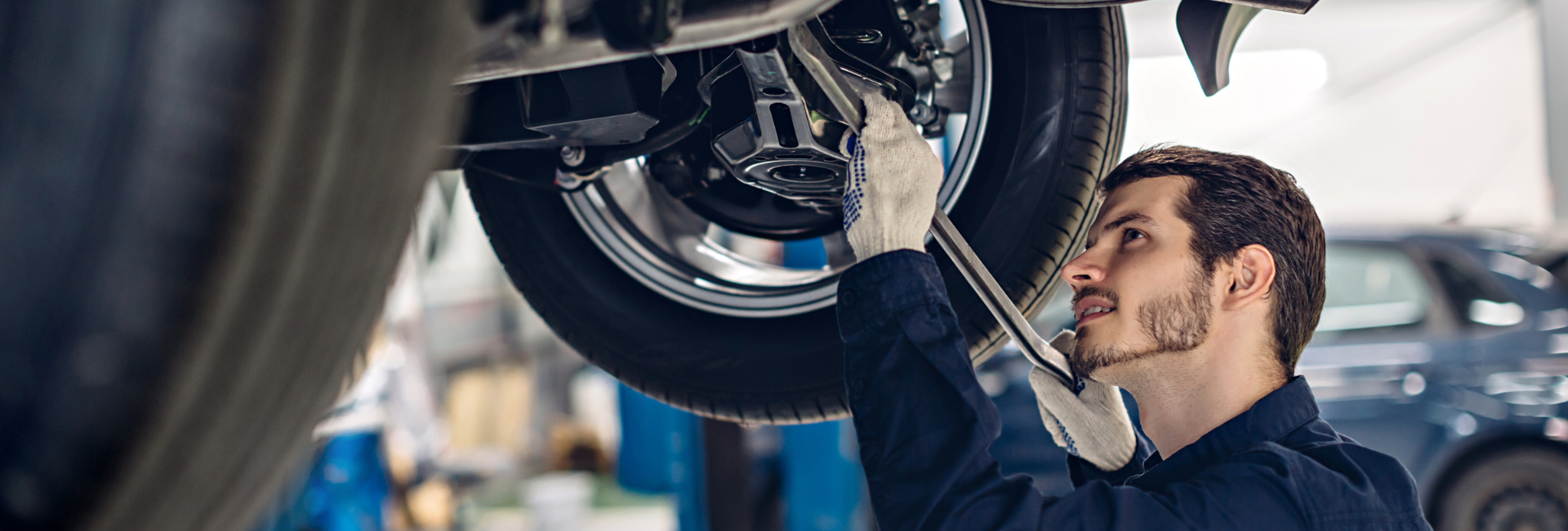
La productividad en el taller
Este es el caso de un cliente de la Garrotxa que tiene un taller mecánico de vehículos además de un servicio de grúa, con un total de diez trabajadores en el taller y seis en el servicio de grúa.
De las dos áreas de negocio, la del servicio de grúa le funcionaba muy bien. Trabajaba para varias compañías aseguradoras que le proporcionaban mucho trabajo y aunque le pagaban precios un poco justos, había optimizado mucho los costos y el rendimiento era bastante satisfactorio. La parte del taller, sin embargo, no funcionaba tan bien, de hecho, estaba dando pérdidas. El cliente nos pidió un análisis de las causas de las pérdidas y nos pusimos a trabajar en ello.
En el taller, con diez trabajadores entre mecánicos y chapistas, se trabajaba de la siguiente manera.
El jefe de taller distribuía las tareas entre los mecánicos y estos, una vez finalizado el trabajo, anotaban manualmente en la orden de trabajo el tiempo dedicado y las piezas utilizadas. El personal administrativo ingresaba esta información en el sistema informático.
Después de pocos días, teníamos suficiente información como para poder analizar en profundidad cuál era el problema que provocaba las pérdidas.
Con la información proporcionada por el cliente, se pudo calcular que la productividad de los empleados del taller era muy irregular. Se calculó la productividad de la siguiente manera: horas trabajadas / horas de presencia en el taller, siendo las «horas trabajadas» las que estaban imputadas a las órdenes de trabajo.
El caso es que con esta información, aún no podíamos determinar cuál era el problema, aunque observamos que la productividad del mejor trabajador era del 87% y la del peor del 43%.
Obviamente, la productividad del 43% era un problema que necesitaba ser analizado aparte, ya que no se podía entender que un empleado solo imputara a las órdenes de trabajo el 43% de su tiempo.
Pero finalmente la productividad media era del 68%, lo que ya nos indicaba un poco el origen del problema pero no lo explicaba del todo.
Para profundizar más, se calculó el ratio de eficiencia de la siguiente manera: horas facturadas / horas trabajadas. Este ratio nos proporcionó más información ya que las horas facturadas son las que repercuten directamente en el estado de pérdidas y ganancias. En una situación ideal, este ratio debería ser del 100%, es decir, todas las horas trabajadas se facturan. Pero la realidad no era esa y al analizar con detalle las imputaciones a las órdenes de trabajo se detectaron los siguientes errores o carencias:
– Errores en las imputaciones a las órdenes de trabajo al poner menos tiempo del dedicado.
– Ineficiencia en la distribución de las tareas a los mecánicos y chapistas debido a una mala praxis del encargado de taller que provocaba «tiempos muertos» entre trabajos, los cuales se imputaban al taller y no se facturaban.
– Reducción manual de las horas imputadas a las órdenes de trabajo por trabajos que se habían prolongado mucho debido a causas imputables al mecánico al no haber resuelto adecuadamente el trabajo.
Finalmente, si se calculaba el ratio de eficiencia (horas facturadas / horas de presencia), el resultado era desastroso.
¿Qué estrategia seguimos para aumentar su productividad?
Se detectó que el trabajador que tenía un 43% de productividad lo era porque se le asignaban tareas para las cuales no estaba preparado. Inicialmente se le asignaron tareas de su nivel y simultáneamente se le hizo un plan de formación que lo preparó para tareas de mayor valor. A los ocho meses, su ratio de productividad había subido hasta el 71%.
Se establecieron protocolos de actuación para las principales reparaciones con el fin de reducir al máximo los errores en los procesos.
Se dotó al taller de más herramientas que facilitaban ciertas reparaciones que hasta ese momento se realizaban con herramientas inadecuadas.
Se instalaron tres pantallas adicionales distribuidas en puntos del taller para que los trabajadores pudieran registrar las horas de las órdenes de trabajo sin tener que desplazarse a la oficina ni llenar papeles manualmente.
Se promocionó a uno de los mecánicos para que pasara a ocupar la posición de jefe de taller, ya que tenía cualidades muy buenas para organizar el trabajo de manera mucho más eficiente. El anterior jefe de taller pasó a ocupar una posición dentro del departamento de grúas.
Al final del ejercicio se pudo verificar que las decisiones que se tomaron hicieron mejorar significativamente el ratio de productividad, que aumentó un 19% hasta el 80,9%, y como consecuencia, esto representó una mejora de los resultados muy importante.
Si tienes un problema económico o financiero en tu empresa, podemos ayudarte a determinar las causas y encontrar las soluciones adecuadas.